The article relates to the technical field of grinding tools with grinding wheels, particularly a diamond roller that is easy to install. The diamond roller is a tool used for shaping and dressing grinding wheels during mass production grinding. Its working principle is as follows: a conventional ceramic grinding wheel is shaped and dressed by the diamond roller installed on the grinding machine, and then after the wheel has been dressed, it grinds the parts, transferring the profile, precision, and dimensions of the diamond roller onto the surface of the parts being processed by the wheel. Currently, each collar of the diamond roller device has multiple collection through-holes communicating with exhaust ring holes for ceramic particles to enter. In the installation process of the diamond roller described in this technical solution, in order to facilitate fitting the roller onto the shaft, the diameter length of the shaft hole is slightly larger than that of the shaft, creating a certain gap between them. When advancing axially along the shaft, if an operator applies force along a non-shaft direction, it can easily cause misalignment of the roller. At this point, using tools like a wooden hammer to readjust can make it difficult for operators to control their applied force and align axially with that of the shaft. Therefore, there is a need for an easy-to-install diamond roller. To address these shortcomings in technology, technicians have provided an easy-to-install diamond roller that reduces operational difficulty during installation and facilitates fitting. The purpose of this invention is achieved through the following technical solution: an easy-to-install diamond roller includes a wheel body and an axial hole passing through it; each mounting hole has two fastening blocks arranged oppositely; opposite sides within each mounting hole have docking grooves that are arranged relative to each other forming an installation position for fitting onto a shaft; additionally, there are drive components radially arranged along mounting holes to drive two fastening blocks closer or further apart. Using this technical method during installation on a shaft involves first fitting the roller onto it and then pushing it down. When stuck, drive components move two fastening blocks closer within their mounting holes; through fasteners' driving force on the shaft, it positions itself within docking grooves formed by two fastening blocks thus realigning itself correctly. Once positioned appropriately, drive components bring both fasteners radially closer until their docking grooves tightly contact with outer walls of shafts securing its position relative to them. Compared to previous methods where adjustments were necessary multiple times for alignment without additional tools reducing operational difficulty while improving efficiency in installation.
In summary, this utility model includes at least one beneficial technical effect:
1. During installation of diamond rollers there’s no need for repeated adjustments as axial alignment can be maintained reducing operational difficulty while enhancing efficiency;
2. The design features an annular rubber layer inside mounting holes which increases friction between diamond rollers and shafts thereby enhancing connection firmness.
The article relates to the technical field of grinding tools with grinding wheels, particularly one that is easy to install.Diamond grinding wheelThe diamond grinding wheel is a tool used for shaping and dressing grinding wheels during mass production. Its working principle is as follows: a conventional ceramic grinding wheel is shaped and dressed using a diamond grinding wheel installed on the grinder, and then the parts are ground after the wheel has been shaped, allowing the profile, precision, and dimensions of the diamond wheel to be replicated onto the surface of the parts being processed by the grinding wheel. Currently, each ring of the diamond grinding wheel device is equipped with multiple collection through-holes communicating with exhaust ring holes for ceramic particles to enter.
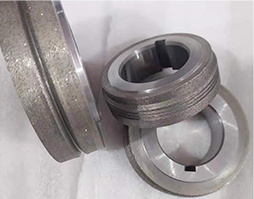
In the installation process of the diamond grinding wheel described in the above technical solution, in order to facilitate fitting the wheel onto the shaft, the diameter of the shaft hole will be slightly larger than that of the shaft, creating a certain gap between them. When advancing along the axial direction of the shaft, if an operator applies force along a non-shaft direction, it can easily cause misalignment of the wheel. At this point, using tools like a wooden hammer to readjust can make it difficult for operators to control applied force and align axially with respect to each other. Therefore, there is a need for an easy-to-install diamond grinding wheel. To address these shortcomings in technology, technicians have provided an easy-to-install diamond grinding wheel that reduces operational difficulty during installation.
In summary, this utility model includes at least one beneficial technical effect:
1. When installing a diamond grinding wheel, there is no need for multiple adjustments; thus, its axial alignment can remain consistent with that of the shaft, reducing operational difficulty and improving installation efficiency.
2. The installation hole is designed with an annular rubber layer which can enhanceDiamond grinding wheelthe friction between it and the shaft, thereby increasing grip strength and ensuring a firm connection between the wheel and shaft.