The application of CVD diamond in gear grinding machine rollers demonstrates the significant driving force of new materials in the machine tool industry. It reminds us to pay attention to the research and application of basic materials, continuously optimizing and enhancing the performance of superhard tools. (1) In the fields of worm wheel grinding machines and forming grinding machines, most diamond rollers used require CVD embedding, whether through sintering or electroplating processes, requiring good bonding strength between CVD diamond and roller substrate, as well as good compatibility with HTHP diamonds to achieve maximum roller lifespan. Given the high cost of CVD diamonds, optimizing the shape design and quantity matching of CVD diamonds is a key focus for their use. (2) In other roller application areas outside gear grinders, CVD diamonds are also increasingly applied, providing excellent reinforcement for weak and easily damaged areas such as roller tips.
Main manufacturing methods of CVD
CVD (Chemical Vapor Deposition diamond) has no metal catalyst compared to high-temperature high-pressure (HTHP) diamonds; its thermal stability and strength are close to that of natural diamonds. Like high-temperature high-pressure synthetic polycrystalline diamonds (PCD), CVD diamond grains are also disordered without brittle cleavage planes, thus exhibiting isotropy. The high hardness and wear resistance of diamonds make diamond films excellent tool materials; CVD diamonds are now also used as cutting tool materials.
As a tool material, CVD diamond has various application forms. The first form involves cutting, grinding, and welding CVD diamond onto the end of tools. Due to this brazing strength being much lower than that between PCD material's diamond layer and hard alloy, its interface connection appears very fragile when applied in intermittent cutting. If the brazing issue with CVD diamonds can be resolved, then CVD diamond cutting materials could compete with PCD materials across all machining fields. Compared to PCDs, this cutting material has advantages such as better thermal stability and longer tool life. The downside is that the cohesive strength between grains is low; thus, it exhibits significant internal stress and brittleness. Additionally, due to a lack of conductivity in CVD diamonds, it hinders their application in electrical discharge machining and polishing techniques. The second form involves fixing CVD diamond films onto substrates through powder metallurgy (sintering method) or electroplating methods; this way allows for a relatively strong bond between CVD diamonds and substrates so they do not fall off during use. This process is mainly applied in grinding wheels and rollers. The third form involves directly depositing a thin layer of CVD diamond onto tool surfaces; this thin film is primarily used for metal cutting tools. Compared to general metal cutting tools, these have advantages such as higher cutting efficiency and better surface finish on workpieces but also have drawbacks: improving adhesion strength on substrate materials is challenging.
There are three typical methods for preparing CVD diamonds:
1.1 Large-area hot wire direct current plasma (HFCVD) preparation method
The hot wire CVD method mixes hydrogen gas with hydrocarbons like methane or acetylene at certain ratios into a reaction chamber where it flows over electrically heated hot wires above 2000°C; at its surface and nearby regions undergoes high-temperature decomposition into atomic hydrogen and various hydrocarbon groups followed by complex adsorption-desorption reactions leading to nucleation/growth on suitable substrate surfaces at appropriate temperatures (700°C-1000°C), forming a diamond coating.
(1) Advantages: The advantage of hot wire method lies in its low preparation cost, simple setup allowing large area deposition easily achieved with good process control.
(2) Disadvantages: The disadvantage is that synthesis speed is slow at about 1-2μm/h with low gas ionization rates leading to lower growth quality for diamond films while being prone to metallic contamination.
1.2 High-power (60-100KW) microwave (MPCVD) preparation method
Microwave plasma chemical vapor deposition (MPCVD) uses quartz tubes or stainless steel resonant cavities as reaction chambers where microwaves pass through waveguides into reaction chambers generating strong alternating electric fields exciting gases into plasma state; hydrogen gas along with methane becomes highly reactive chemical groups diffusing onto suitable substrate surfaces depositing out diamond coatings.
(1) Advantages: Microwave plasma represents an electrode-less discharge excitation mode producing very pure plasma avoiding contamination from electrodes/reactor walls while achieving very high atomic hydrogen concentrations due to stable microwave discharge resulting in relatively higher quality deposited diamond coatings.
(2) Disadvantages: A prominent drawback here includes low preparation efficiency along with expensive equipment leading higher production costs making it difficult to scale up MPCVD deposition areas.
1.3 Direct current arc plasma jet (DCArcplasmajet CVD) preparation method
This method introduces certain DC voltage across positive/negative circuit poles causing gas flowing between them being discharged igniting an arc which rapidly heats gases up reaching extremely high temperatures causing rapid expansion ejecting out high-temperature plasma jets from nozzles while substrates must be forced cooled via water generally placed below plasma torch using mixtures like hydrogen/argon/methane as source gases where hydrogen/methane serve common raw gases for depositing diamond coatings while argon ignites/maintains arc discharge.
(1) Advantages: This represents a typical fast deposition approach maintaining record fast deposition rates at 930μm/h ensuring sufficient ionization providing very high atomic hydrogen concentrations balancing both deposition rate/diamond coating quality making it promising technology for industrial applications.
(2) Disadvantages: However this preparation consumes large amounts energy/gas leading higher production costs requiring gas recycling/reducing power consumption lowering costs making it more competitive in market conditions.
The quality ranking among three manufacturing processes producing CVDDiamonds follows: microwave process > direct current arc process > hot wire process while costs rank inversely; recently improvements made on hot wire processes have led newly developed hot wire produced CVDDiamonds mechanical properties nearing those produced via arc processes.
CVD Diamonds Application in Worm Gear Grinding Machine Diamond Rollers
Worm gear grinding machines serve continuous generating grinding machines suitable for mass production/specialized gear processing featuring basic processes using Diamond rollers dressing worm wheels followed by worm wheels grinding gears requiring precision/lifespan from Diamond rollers during operations .
The principle behind worm wheel grinder’s gear grinding resembles engagement principles found within pairs spiral gears where worm wheel essentially acts like spiral gear having few teeth(single head wheel teeth count equals one). Due its fewer teeth having larger spiral angles long teeth wrapping around axis many times forming involute worms whose normal base equals normal base gears being ground . Engagement between worm wheel grinder/wheels viewed akin imaginary rack formed along normal cross-section processed gears/worm wheels shown figure 1 .
During worm wheel grinder’s operation ,grinding wheel profiles continuously wear down generally needing dressing after processing several dozen pieces due differences among abrasive types/bonding agents/concentration etc requiring dressing using Diamond rollers . Worm Diamond Roller serves core component within worm grinders designed according specific requirements based upon ground gears such standard involute ,crown tooth ,chamfered tooth etc necessitating corresponding shapes designed/fabricated accordingly shown figure 2 depicting common shapes suited different models grinders . Its outer circular portion represents vulnerable area where gear module ranges from 0 .5mm -10mm thickness varies from 0 .35mm -5mm respectively .
For instance standard involute cylindrical gear module m=0 .5mm requires outer circular thickness only 0 .35mm presenting huge challenges traditional electroplated/sintered Diamond roller lifespans ; embedding/fixing CVDDiamond via sintering/electroplating greatly enhances weak links increasing lifespans significantly now mainstream market’s worm wheel grinders utilize tip sections(Circular outer parts ) embedded CVDDiamonds technology shown figure 3 depicting morphology embedded CVDDiamonds within Worm Rollers .
Such rollers typically select DC Arc Plasma Jet/CVDDiamond Hot Wire technologies since Microwave Plasma CVDDiamonds remain prohibitively expensive under circumstances meeting roller requirements DC Arc Plasma Jet/CVDDiamond Hot Wire technologies generally preferred over Microwave Plasma options ; thickness typically ranges from 0 .5mm -1 .2 mm cut laser shaped per required specifications embedding CVDDiamonds supporting each other enhancing strengths outer circular/sloped portions effectively utilized together supporting each other enhancing strengths outer circular/sloped portions effectively utilized together supporting each other enhancing strengths outer circular/sloped portions effectively utilized together supporting each other enhancing strengths outer circular/sloped portions effectively utilized together supporting each other enhancing strengths outer circular/sloped portions effectively utilized together supporting each other enhancing strengths outer circular/sloped portions effectively utilized together supporting each other enhancing strengths outer circular/sloped portions effectively utilized together supporting each other enhancing strengths outer circular/sloped portions effectively utilized together supporting each other enhancing strengths outer circular/sloped portions effectively utilized together supporting each other enhancing strengths outer circular/sloped portions effectively utilized together supporting each other enhancing strengths outer circular/sloped portions effectively utilized together supporting each other enhancing strengths outer circular/sloped portions effectively utilized together supporting each other enhancing strengths outer circular/sloped portions effectively utilized together supportin...
Main manufacturing methods of CVD
Compared to high-temperature high-pressure (HTHP) diamonds, CVD (Chemical Vapor Deposition diamond) does not use metal catalysts, and its thermal stability and strength are close to that of natural diamonds. Like high-temperature high-pressure synthetic polycrystalline diamonds (PCD), CVD diamond grains are also arranged in a disordered manner, without brittle cleavage planes, thus exhibiting isotropy. The high hardness and wear resistance of diamonds make diamond films excellent tool materials, and CVD diamonds are now also used as a type of cutting tool material.
As a tool material, CVD diamond has various application forms. The first form is cutting and grinding the CVD diamond and welding it to the end of the tool. Due to the much lower brazing strength compared to the bonding strength between PCD material's diamond layer and hard alloy, its interface connection appears very fragile when applied in intermittent cutting. If the brazing issue of CVD diamonds can be resolved, then CVD diamond cutting tools will be able to compete with PCD materials across the entire machining field. This type of tool material has advantages over PCD in terms of good thermal stability and long tool life. The disadvantages include low cohesive strength between grains, resulting in significant internal stress and brittleness in the material. Additionally, due to the lack of conductivity in CVD diamonds, their application in electrical discharge machining and polishing techniques is hindered. The second form involves fixing CVD diamond films onto substrates through powder metallurgy (sintering) or electroplating methods; this method allows for a relatively strong bond between the CVD diamond and substrate so that it does not fall off during use. This process is mainly applied in grinding wheels and rollers. The third form involves directly depositing CVD diamond films onto the surface of tools; these films are thinner and mainly used for metal cutting tools. Compared to general metal cutting tools, this type has advantages such as higher cutting efficiency and better surface finish on workpieces. However, this method also has drawbacks: improving adhesion of deposited thin films to substrate materials is challenging.
There are three typical methods for preparing CVD diamonds:
1.1 Large-area hot wire direct current plasma (HFCVD) preparation method
The hot wire CVD method involves mixing hydrogen gas with hydrocarbons like methane or acetylene in certain proportions into a reaction chamber where it flows past electrically heated hot wires at temperatures above 2000°C; at their surface and nearby areas, these gases decompose into atomic hydrogen and various hydrocarbon groups at high temperatures followed by complex adsorption-desorption reactions leading to nucleation and growth on suitable substrate surfaces at appropriate temperatures (700°C - 1000°C), forming a diamond coating.
(1) Advantages: The advantage of the hot wire method lies in its low preparation cost, simple apparatus, ease of achieving large-area deposition, and good process control.
(2) Disadvantages: The disadvantage of the hot wire method is that its synthesis speed is relatively slow at about 1-2μm/h; gas ionization rates are low; growth quality of diamond films is not very high; it can also easily lead to metal contamination.
1.2 High-power (60-100KW) microwave (MPCVD) preparation method
Microwave plasma chemical vapor deposition (MPCVD) uses quartz tubes or stainless steel resonant cavities as reaction chambers where microwaves pass through waveguides into reaction chambers creating a strong alternating electric field that excites gases into plasma; hydrogen gas and methane become highly reactive chemical active groups which diffuse onto suitable substrate surfaces depositing diamond coatings.
(1) Advantages: Microwave plasma is an electrode-less discharge excitation mode producing very pure plasma avoiding contamination from electrodes or reactor walls; microwave plasma has high energy density with considerable electron temperature allowing for very high atomic hydrogen concentrations while being particularly stable thus yielding relatively higher quality deposited diamond coatings.
(2) Disadvantages: A prominent drawback of this deposition method is low preparation efficiency along with expensive equipment costs making it difficult to scale up MPCVD diamond film deposition areas.
1.3 Direct current arc plasma jet (DCArcplasmajet CVD) preparation method
This preparation method involves applying a certain direct current voltage between positive and negative electrodes causing gas flowing between them to be discharged igniting an electric arc which rapidly heats gases to extremely high temperatures causing them to expand rapidly ejecting high-temperature plasma jets from nozzles; substrates must be forcibly cooled by water generally placed below the plasma torch using mixtures of hydrogen gas, argon gas, and methane as source gases for deposition where hydrogen gas along with methane serves as common source gases for depositing diamond coatings while argon ignites arcs maintaining discharge.
(1) Advantages: This is a typical high-speed deposition method maintaining currently known fastest deposition rate at about 930μm/h; ionization within plasmas is thorough providing very high atomic hydrogen concentrations thus balancing both deposition rates with quality making it considered an industrially promising technology for preparing diamond films.
(2) Disadvantages: However, this preparation method consumes large amounts of gas and electricity leading to higher production costs requiring measures like gas recycling or reducing power consumption for cost reduction making it more competitive in markets.
The quality ranking order for CVD diamonds produced by these three manufacturing processes is: microwave process > direct current arc process > hot wire process while costs rank inversely; recent improvements have made mechanical properties from new hot wire processes approach those produced by arc processes.
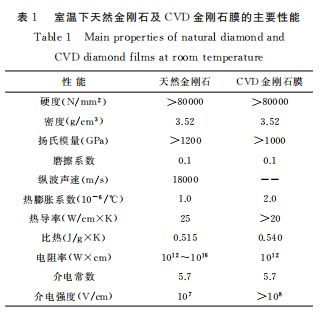
The worm gear grinding machine, as a continuous generating grinding machine for straight and helical cylindrical gears, is suitable for mass and specialized gear processing production. The basic process involves using a diamond roller to dress the worm grinding wheel, followed by grinding the gear with the worm wheel. The grinding process has high requirements for the precision and lifespan of the diamond roller.
The principle of gear grinding with a worm wheel is equivalent to the meshing principle of a pair of helical gears. The worm wheel can essentially be seen as a helical gear with very few teeth (the number of teeth on a single head wheel equals 1). Due to its few teeth, large helix angle, and long teeth that can wrap around the axis many times, it forms an involute worm whose normal base circle equals that of the ground gear. The meshing between the worm wheel and the gear is regarded as the engagement of an imaginary rack formed along the normal cross-section of both during processing, as shown in Figure 1.
During the grinding process with a worm wheel, the profile of the wheel continuously wears down. Generally, due to differences in abrasive types, bonding agents, abrasive concentrations, and variations in ground gears, after grinding several to dozens of gears, it becomes necessary to dress the worm wheel. Dressing requires using a diamond roller specifically designed for worms. The diamond roller is a core component of the worm gear grinder; based on specific requirements such as standard involute profiles or bevel gears, it needs to be designed and processed into corresponding shapes. Figure 2 shows common shapes of diamond rollers suitable for different models of gear grinders. The outer circular part is where wear occurs; gear module sizes range from 0.5 mm to 10 mm with outer circular thicknesses varying from 0.35 mm to 5 mm.
For example, a standard involute cylindrical gear with a module m = 0.5 mm requires an outer circular thickness of only 0.35 mm for its roller; such dimensions pose significant challenges for traditional electroplated or sintered diamond rollers' lifespan. By embedding CVD diamonds into and fixing them onto the outer circle through sintering or electroplating processes, we can significantly strengthen weak points in rollers and greatly increase their lifespan. Currently, mainstream rollers used in worm wheel grinders adopt CVD diamonds embedded at their tips (outer circles). Figure 3 shows images of CVD diamonds embedded in worm rollers.
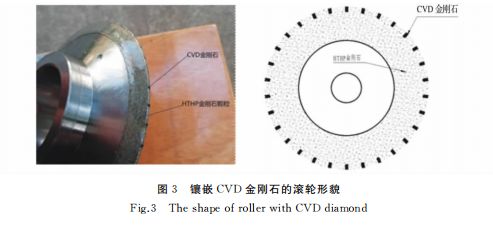
Such rollers generally use DC arc plasma-sprayed CVD diamonds or hot wire process CVD diamonds; microwave plasma CVD diamonds are usually not selected due to their high cost when DC arc plasma-sprayed or hot wire process CVD diamonds can meet roller requirements. The thickness of CVD diamonds typically ranges from 0.5 mm to 1.2 mm and is laser-cut into required shapes based on roller specifications. Embedding CVD diamonds supports each other with HTHP diamonds effectively enhancing strength at both outer circular parts and inclined surfaces.
0
Application of CVD Diamonds in Forming Grinding Machine Diamond Rollers
The forming wheels used in forming grinders are shaped by forming tools within axial cross-sections; these wheels can feed vertically during operation. The ground gears are supported by dividing heads and tailstocks while moving longitudinally back-and-forth on worktables to grind tooth surfaces; after each tooth is ground, indexing occurs. In machines that grind helical gears, wheels can rotate at angles according to workpiece helix angles while simultaneously undergoing reciprocating motion for additional rotation; if machine tool wheel frames allow wheels to enter internal tooth workpieces, internal gears can also be ground. Forming grinders have simple structures with high efficiency and precision up to grade five; they are particularly suitable for batch production involving gears with fewer than seventeen teeth.
Forming grinder wheels are generally manufactured using sintering or electroplating processes; early forming grinder wheels lacked reinforcement from CVD diamonds—edges (arcs) only had HTHP diamond particles leading to rapid curve wear during use. After strengthening through embedding CVD diamonds technology, curve retention significantly improves.
Application of CVD Diamonds in Other Rollers
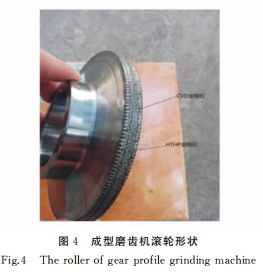
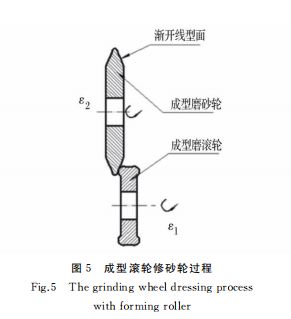
0
With rapid development in forming grinding technology and widespread application of forming grinding wheels across various fields such as crankshafts, piston ring grooves, bearings, steering joints, hydraulic valve components etc., there has been extensive usage observed. To maintain original precision during use over time requires increasingly higher standards for dressing tools previously used single-point dressing pens which provided poor accuracy and low efficiency compared to modern solutions like complex-shaped diamond rollers that match forming grinding wheels allowing high-speed precise dressing.
In forming grinder operations where curved surfaces are involved during sanding processes sharp edges represent weak points which could also benefit from embedding techniques using CVD diamonds greatly extending roller lifespans as illustrated by Figures six showing applications while figure seven depicts schematic representations regarding dressing processes.
Conclusion
The application of CVD diamonds within gear grinder rollers demonstrates significant advancements brought about by new materials within machine tool industries reminding us about importance placed upon foundational material research alongside continual optimization efforts aimed towards enhancing superhard tool performance: (1) In both worm-wheel grinders & shaping machines most utilized diamond rollers require embedding via either sintering/electroplating methods ensuring strong adhesion between them & base materials while achieving optimal compatibility alongside HTHP variants maximizing overall longevity potential given high costs associated thus focusing on optimizing designs/quantity matching becomes paramount when utilizing said resources effectively.(2) Beyond just milling applications other areas involving different types also see increasing adoption rates benefiting vulnerable areas like sharp corners etc.
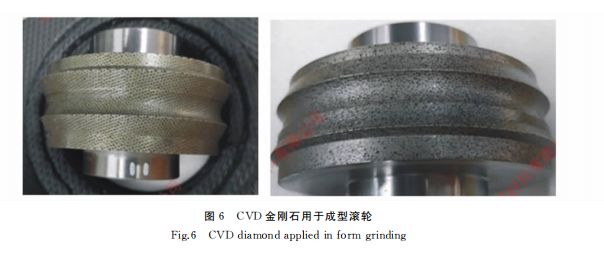
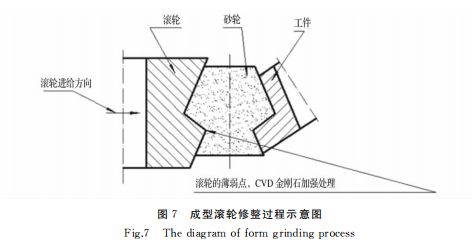
CVD金刚石在齿轮磨床滚轮中的应用,显示了新材料对机床工具行业巨大的推动作用。提示我们要重视基础材料的研究和应用,不断优化提升超硬工具性能。(1)在蜗杆砂轮磨齿机和成型磨齿机领域, 所使用的金刚石滚轮绝大部分要求镶嵌CVD,无论是烧结工艺还是电镀工艺,要求CVD金刚石与滚轮基体有较好的结合力,与 HTHP金刚石有较好的匹配,能达到滚轮的最大寿命。鉴于CVD金刚石价格较高,优化CVD金刚石形状设计和数量匹配是CVD使用的重点。(2)在磨齿机之外的其他滚轮应用领域,CVD金刚石也得到了越来越多的应用,对滚轮尖角等薄弱易损部位有很好的强化作用。
In the field of superhard tools, CVD diamond, combined with traditional processes, plays an increasingly prominent role in helping superhard products move towards high-end and upgrade through its unique performance.